Weighing and Batching – Case Studies
Resin Dosing System
Client: Manufacturing and Selling of Refractories and Monolithic for iron and steel industry.
Year of Installation: 2021
Location: Odisha, India
Client’s Requirement: To Design, Supply, Test supervise installation and commission a Resin dosing system.
Challenges:
- To overcome the wastage and inaccurate weighing.
- To avoid heating issue.
- Total dust free operation.
- Precise quantity of chemical is transferred to mixer.
- Solution for actuating the entire process.
Solution:
MELSS has offered a liquid batching solution, which is specially designed to operate Resin Dosing System.
- Flow adjustment depending on the application.
- Weigh hopper is provided for accurate weighing
- No need to worry about mixing proportion.
- Required quantity of resin is fed into the mixer through the weigh hopper based on the selected recipe.
- PLC panel with HMI is provided for actuating the entire operation.
- Manual valve is provided for maintenance purposes.
Resin Dosing System Has:
- DAY TANK
- WEIGH HOPPER
- WEIGH HOPPER MOUNTIG STRUCTURES
- LOAD CELL ARRANGEMENT
- CONTROL VALVE
- PUMP ASSEMBLY
- BRAIDED HOSE ARRANGEMENTS
- 7’’ HMI
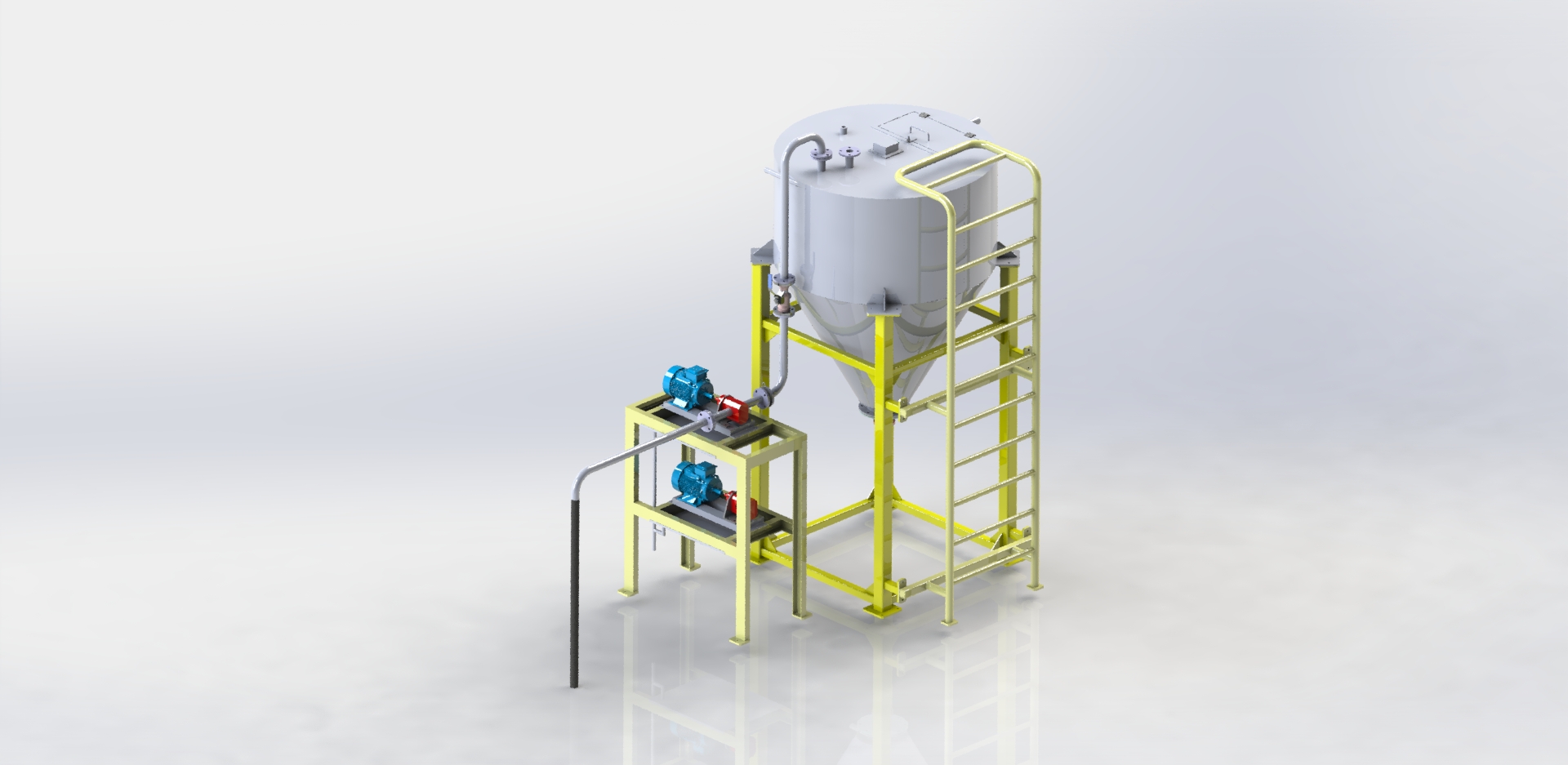
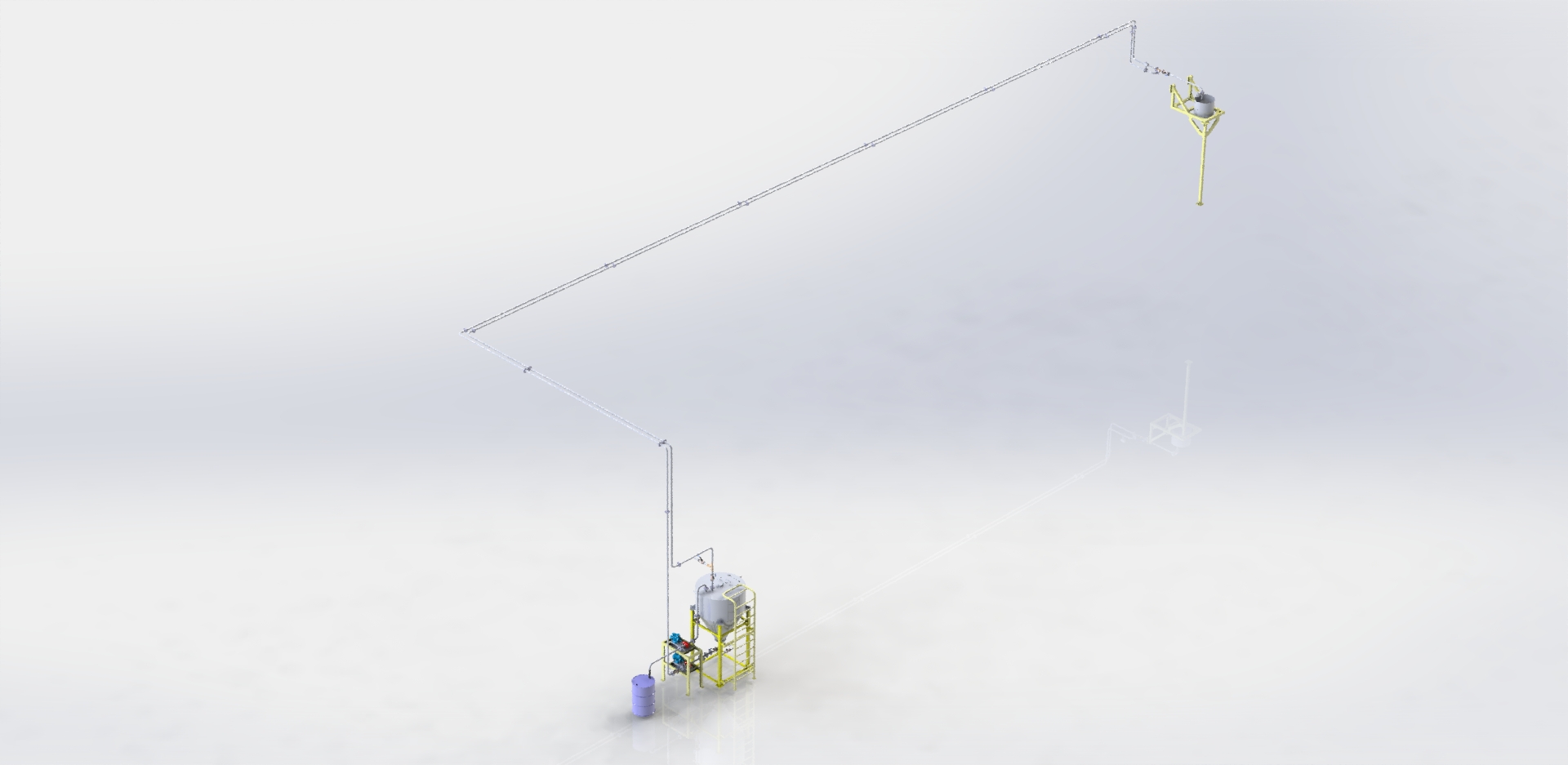
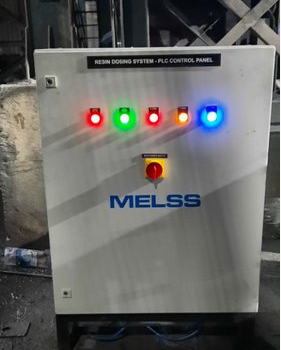
Over View:
The day tank has capacity of 1000 Liters, Resin from 250 litres barrel is transferred to day tank by the resin transfer pump. Similarly, the resin from day tank to weigh hopper is transferred through gear pump. Weigh Hopper has capacity of 140 litres and has mounting bolts and nuts along with 3-point load cell arrangement. The resin is transferred in the SS pipe line and discharged into the weigh hoppers through the automated coarse and fine valve which controls the quantity of discharge into the weigh hopper. Resin from weigh hopper is discharged into the Mixer through automated shut off valve and required quantity of Resin from the day tank is fed into the mixer through the weigh hopper based on the selected recipe. Pipes from the day tank to the weigh hopper will be supported by clamps and structure. PLC panel with HMI is provided for actuating the entire operation and we have provided manual valve for maintenance purposes. The left-over resins in the pipeline are fed back to the day tank through return line. Day tank should be drained out completely before plan for continuous shutdown.
Customer Benefits: We gave the high accuracy, hygienic and time minimizing solution to our client.